February 14, 2024
3D-powered efficiency – how VARD delivered a ship design in just 10 weeks
Teams at VARD Design & Engineering were faced with a major challenge: could they slash the typical structural design time by a third, and go from contract signing to class package in 10 weeks? Equipped with NAPA’s 3D based tools, they rose to the occasion by working smartly, creatively, and collaboratively. Here’s how they achieved this masterstroke of speed and precision.
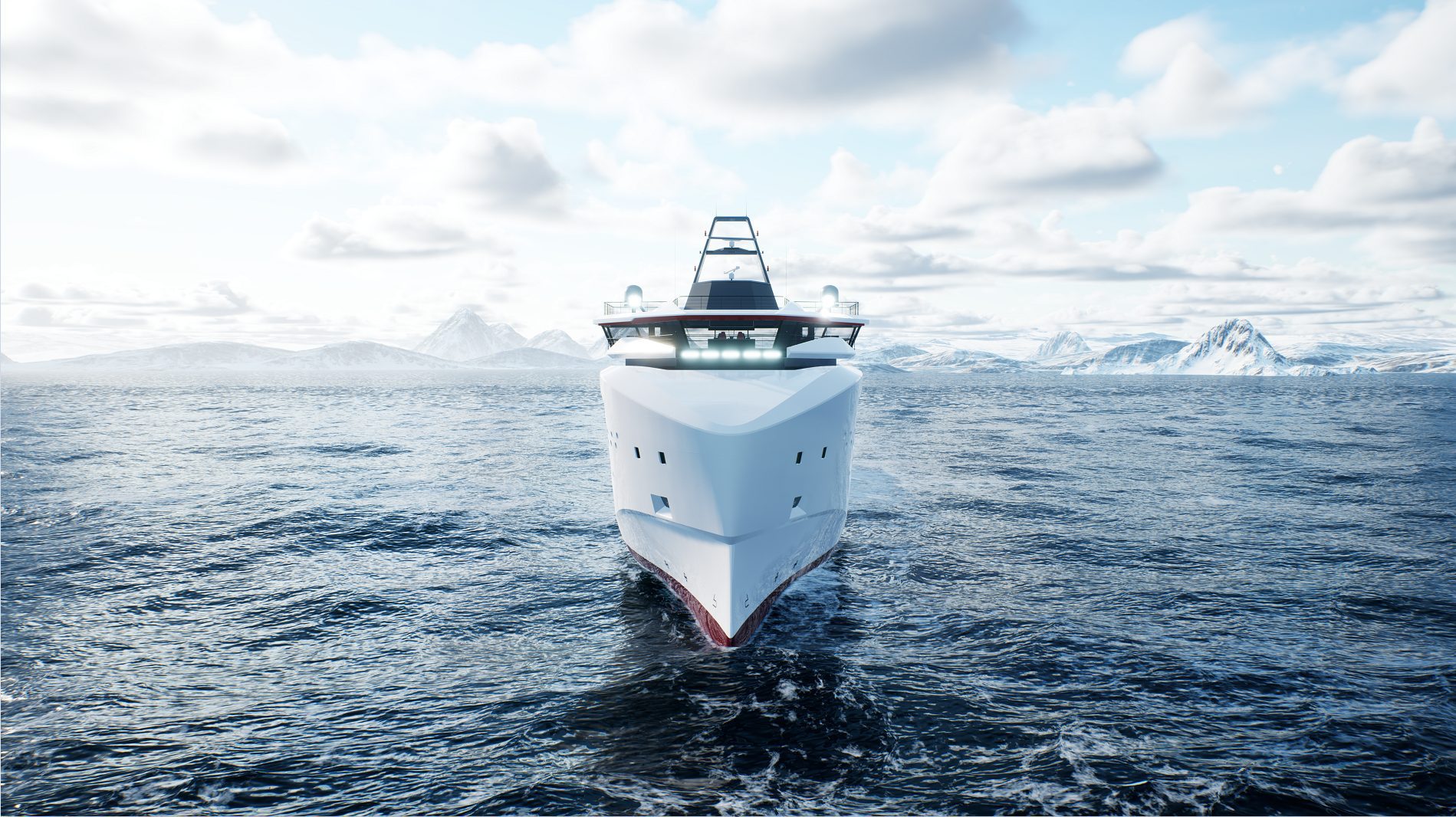
Shipbuilding is in a state of flux. The legislative push for vessels to be cleaner and safer is forcing often radical design changes. Timescales for deliveries are also shortening, with the result that designers are having to do more and in less time.
This challenges traditional, linear design processes and drives a need for greater design certainties at an earlier stage. It has created the requirement for a new generation of design tools which enable concurrent working by multiple disciplines, all of whom have access to a ‘single source of truth’ – a model hosted in a digital 3D environment.
NAPA has been in the vanguard, providing the industry with a range of tools, including structural design. Just how this can transform and accelerate the structural design process is illustrated by the recent completion — in 10 weeks — of a class package by the team at VARD Design & Engineering. This shaved something between four and six weeks off the usual process.
Distributed and collaborative engineering
The company turned a challenge into an opportunity. It had an available building slot in one of its shipyards and the opportunity to deliver a wind support vessel based on a design from its 4 19 series for the offshore renewables sector. However, the time available to get a class package completed was less than ideal: going from the usual 14-16 weeks down to 10 required some creative thinking and cooperation from both the design team and the class society. It was the essential foundation for this collaborative and streamlined process to happen in reality.
VARD’s main engineering office is in Ålesund, Norway, and the company has a total of 22 locations in 11 countries. With its sites and specialisms so geographically spread out, the company operates a distributed engineering model, enabling it to be agile especially in the face of tight time constraints. To deliver the wind support vessel in 10 weeks, for example, engineers from the design office in Croatia were flown into Ålesund to complete one set of tasks at the same time as others from the engineering office in Tulcea, Romania were carrying out modeling work.
The central role of digital tools
NAPA’s structural design solutions facilitated, from the earliest stage, the creation of a 3D model with the structural details necessary for pre-coordination. Colleagues in the machinery and piping departments could be working in parallel, with the vessel’s structure being adapted as necessary on an ongoing basis.
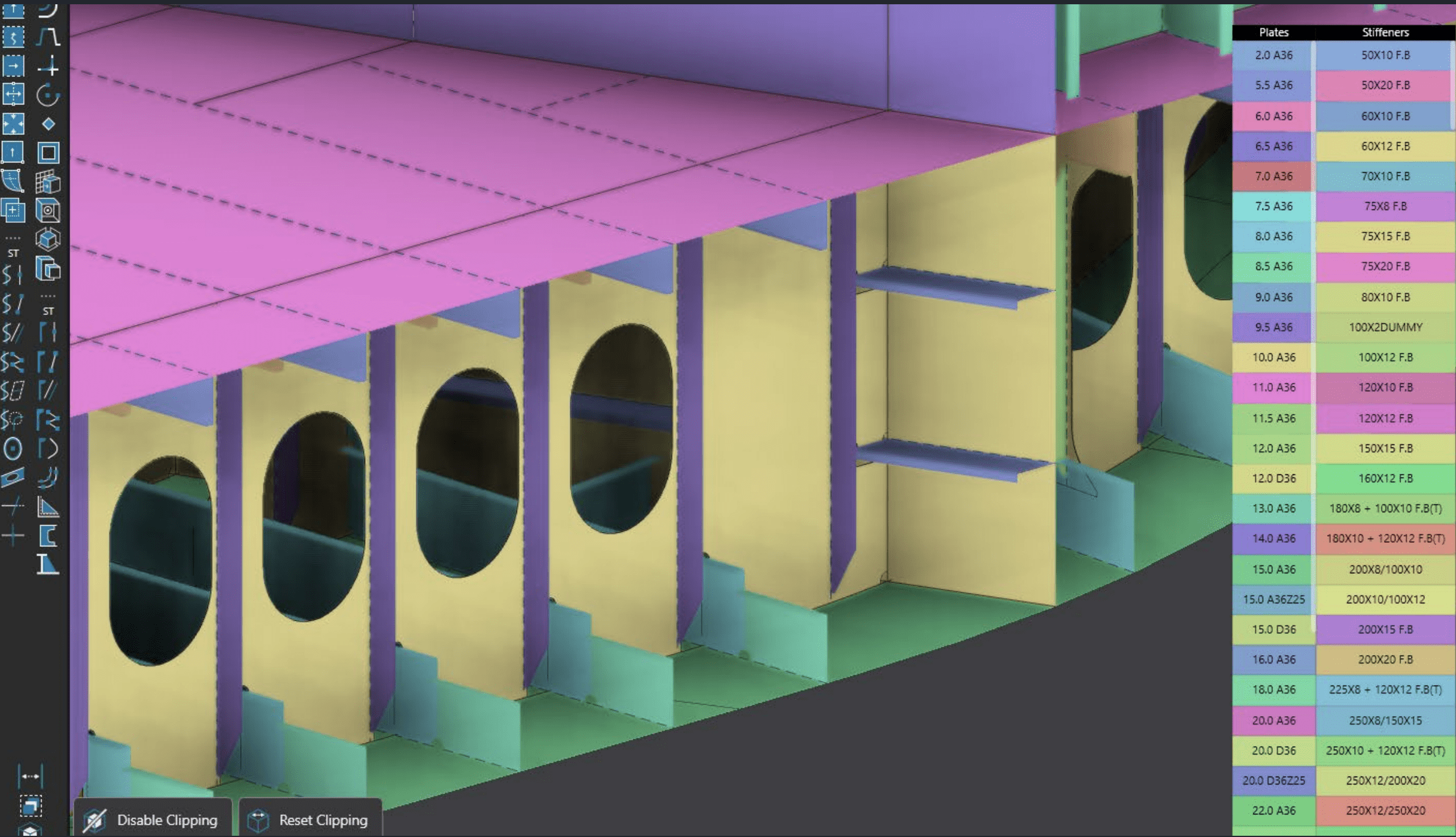
With NAPA, we have a 3D tool that enables us to look at a vessel from the big perspective but also at the detail level. That enables us to have good insight in Ålesund and pick out problem areas before they become an issue for the yards. — Lina Austigard, Senior Engineer with VARD Design & Engineering
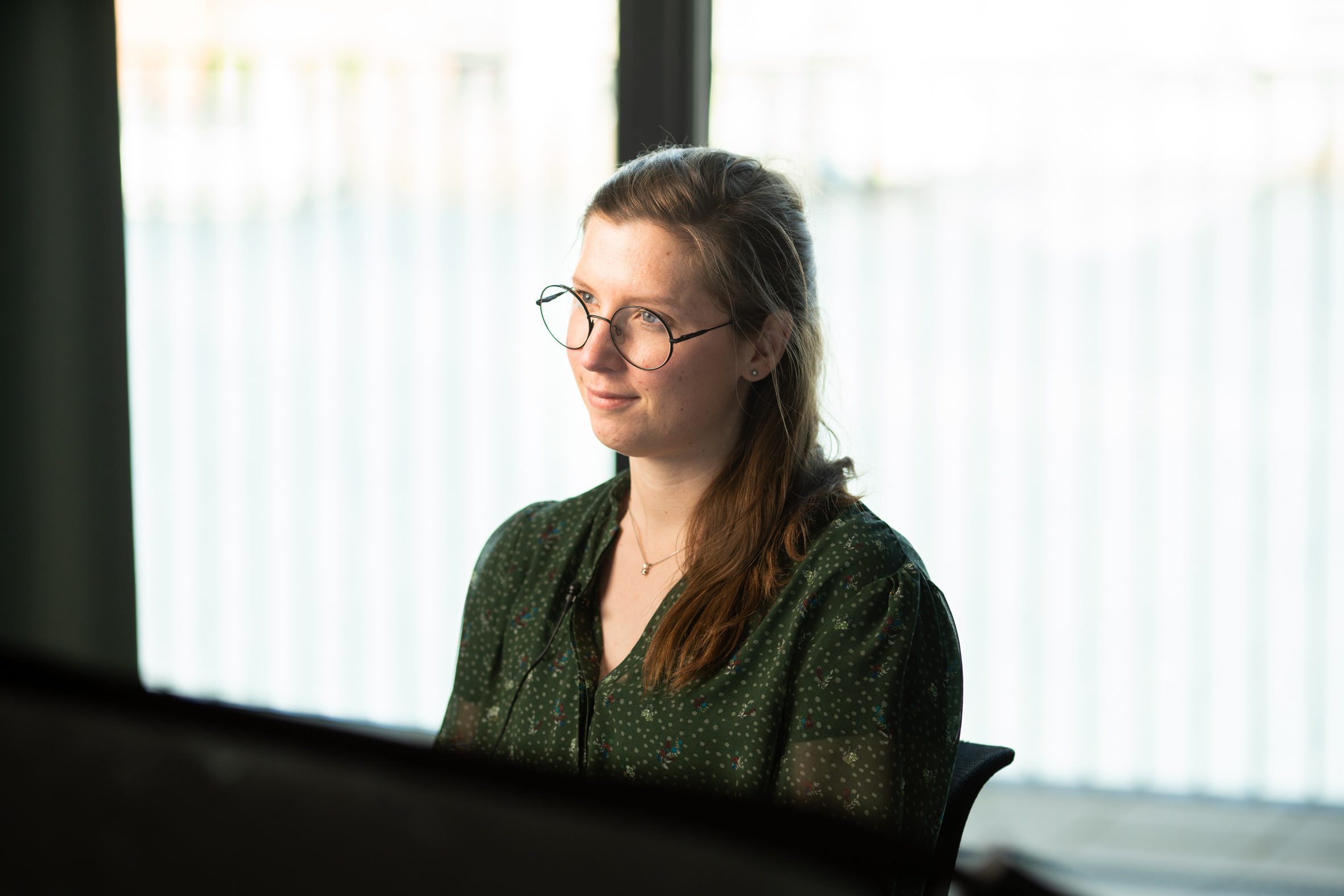
Ms Austigard highlights that as time pressures mount, being able to start detailed design earlier is a key advantage.
NAPA is the live backdrop that makes it possible. You’re able to pick up flaws that you wouldn’t necessarily catch in 2D, such as where you have misalignments or rooms that aren’t buildable because the geometries don’t fit in the real world.
Capturing individual requirements
Even with a typical class package timescale of 14-16 weeks, there will remain a lot of communication between the design team and the yard in terms of getting detail work done. The development of an actual vessel still requires a lot of time and even sister vessels can have notable variations.
Different clients within the same market segment will have different requirements, Lina Austigard notes. For example, wind support vessels typically have a large gangway and at least one large crane but clients will have preferences for the type of gangway, precisely how it is used, and how many cranes and other pieces of equipment they have. They may also have different requirements in terms of accommodation — how many people are living onboard, and to what standard.
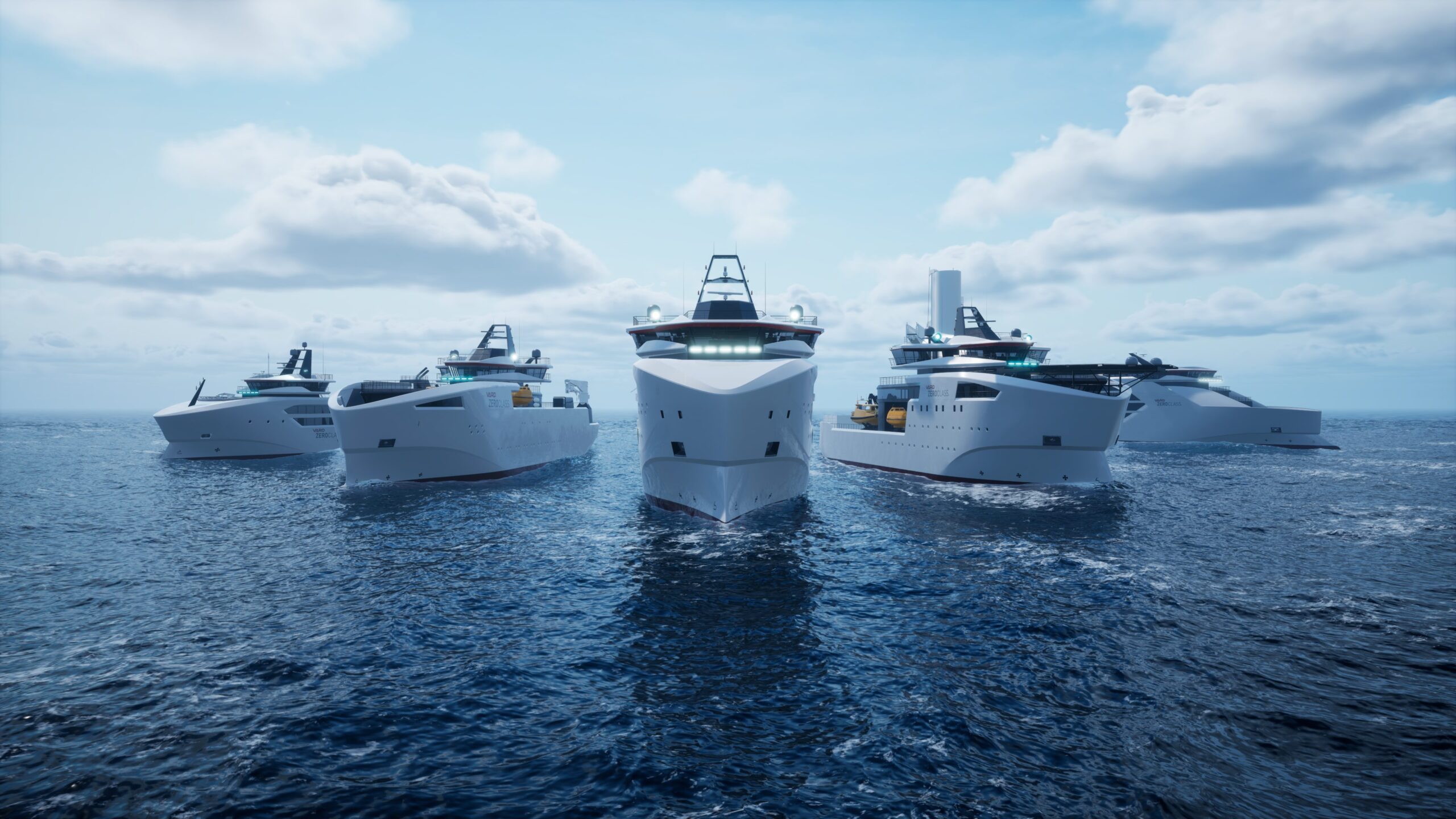
“More and more, we’re seeing clients looking to get ready for newer types of fuels. We find ourselves building “fuel-ready” vessels that will allow a switch to new fuels when the technology is ready,” she says.
Partnership with NAPA
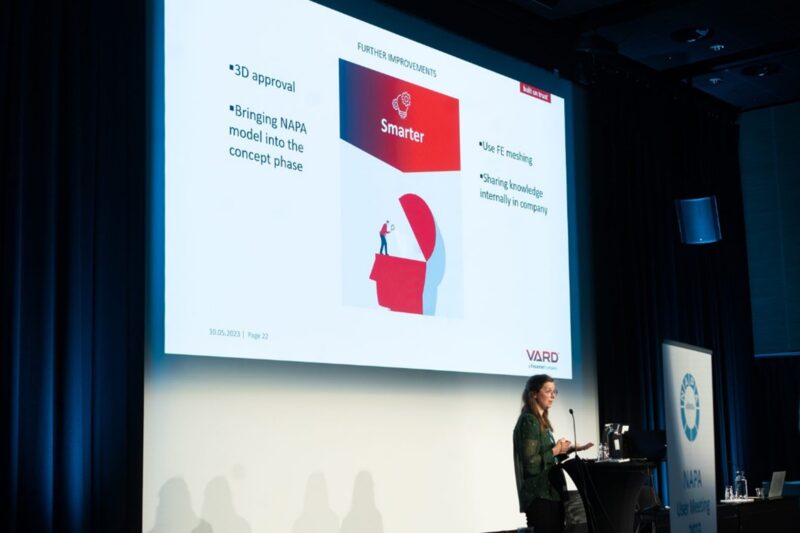
A close relationship with the NAPA team has been another key enabler. Especially in the early months following the implementation of NAPA Steel, timely support, including provision of training videos and scripts, enabled VARD to quickly achieve the competency and the confidence needed to take on challenges. Such a relationship will be central as efforts to save time intensify, with a need to also guarantee the quality and performance of new designs.