September 20, 2022
Information hub: Advancing ship design innovation and solving practical challenges
From automated design optimization and information sharing, to a fully 3D design and approval process, we’re constantly working with our partners to find new ways to improve the design process.
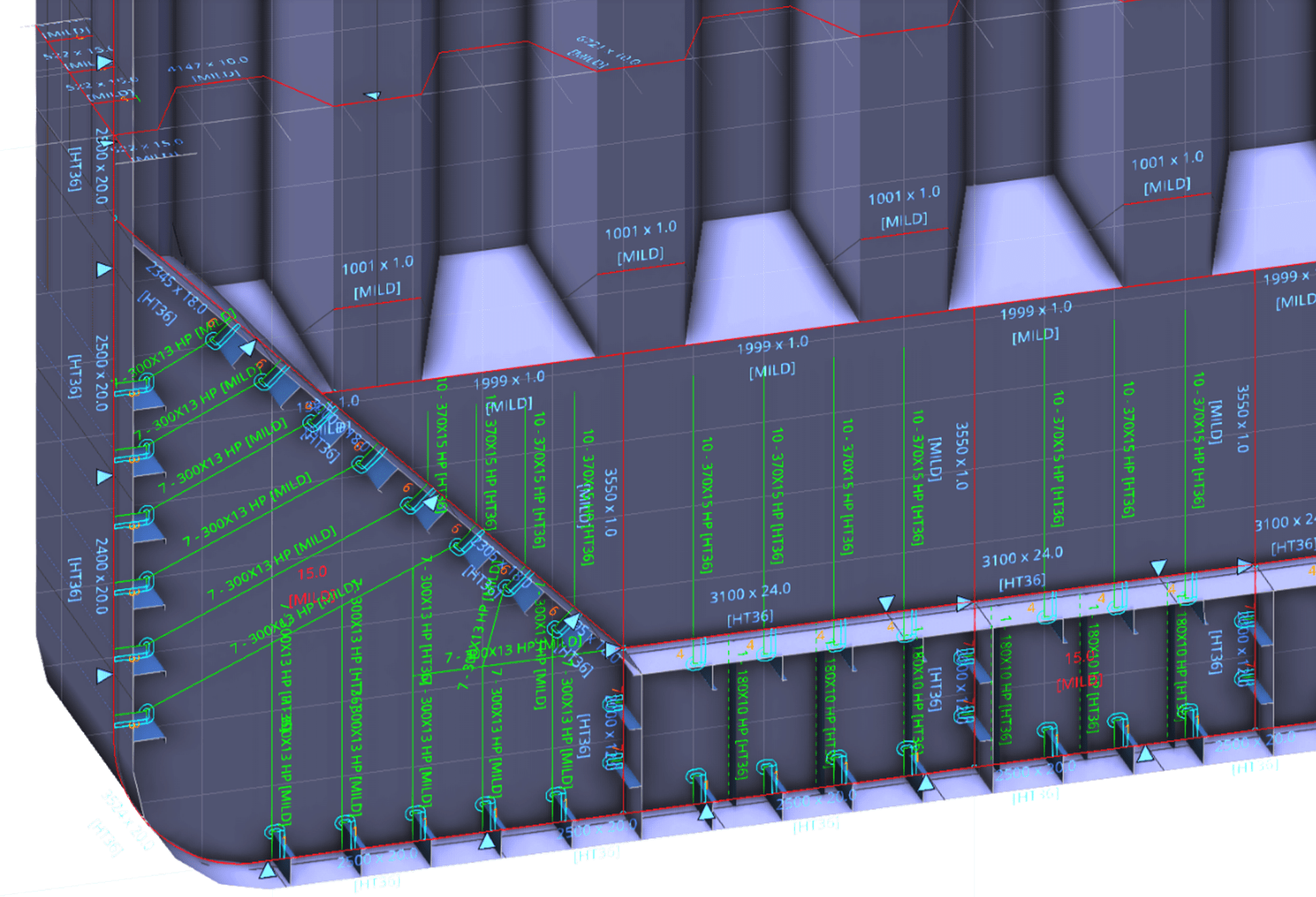