August 25, 2021
Fincantieri: Staying ahead of the pack
Fincantieri is one of the world’s leading shipyards. Since 1995 it has used NAPA to streamline its design process, and the partnership is still driving innovation today.
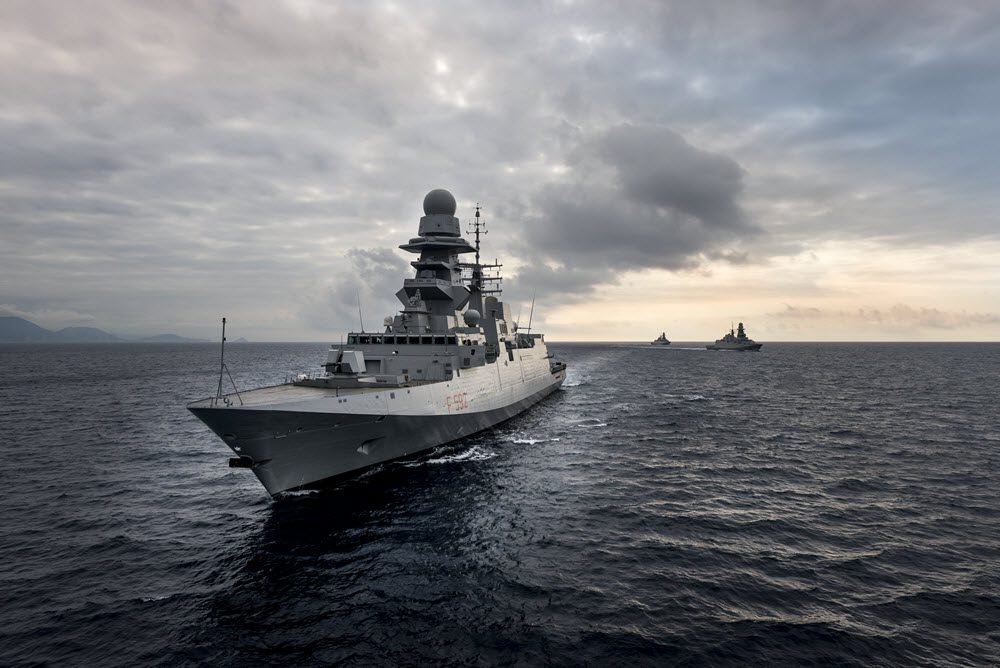
How Fincantieri has used NAPA Steel to stay ahead of the competition for 18 years?
Background
Fincantieri’s naval division designs and delivers a wide variety of naval vessels, including frigates, corvettes, destroyers, patrol vessels, as well as aircraft carriers and submarines. Based in Genoa, Italy, they are the key supplier for the Italian navy, while also serving several other navies globally.
Fincantieri started using NAPA for naval architectural calculations in 1995. Six years later in 2001, NAPA Steel was introduced in Fincantieri’s Design Center in Trieste. In 2003, following its Trieste merchant ship division for cruise ship design, the naval division in Genoa adopted NAPA Steel.
This made Fincantieri a forerunner in using 3D models to maintain consistency between 2D and 3D representations of ship design. At the time, due to the purely graphical nature of the software, 2D information was superimposed to the 3D representation – which meant the consistency was ensured by manual checks.
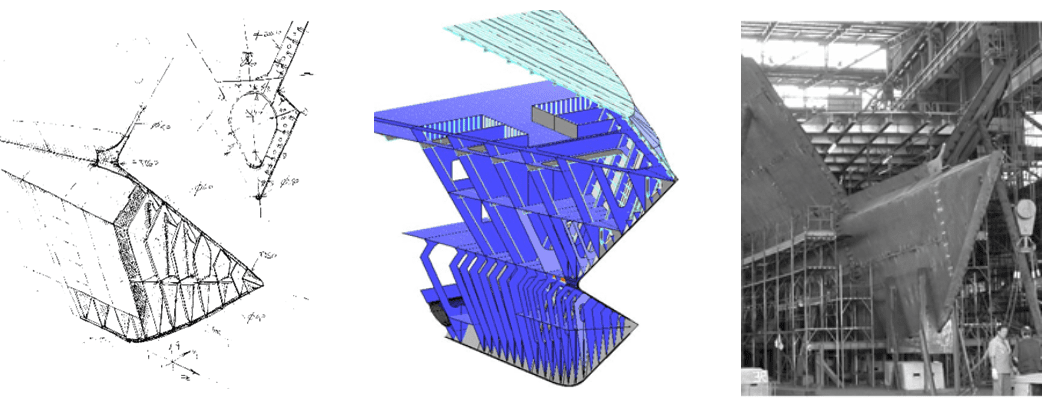
Since then, NAPA and Fincantieri have continuously developed and evolved the software and process, resulting in processes that are leaner and more reliable, and provided unique tools specifically for naval vessel designs.
Challenge
Fincantieri engineers had a dream of changing the daily work from 2D to 3D. Over the next two decades, challenges have changed, but the principles have remained the same; ship design requires different idealizations of the ship object. As simple as possible to perform calculations yet as close to reality to solve problems. Finding the equilibrium among these requirements, timing and resource is the challenge for every end-user that NAPA solves, and one to which Fincantieri’s users have contributed collaboratively.
As software capabilities have developed, a key challenge to solve has been to make the most of 3D models – to use the same models throughout the design process as much as possible, while accommodating frequent revisions, changes and updates.
As soon as the modelling capabilities of NAPA Steel expanded, the possibility to generate three-dimensional scenarios was used to develop machinery and auxiliary system arrangements in the early design stages. With naval vessels typically limited for space and full of equipment, optimising space for auxiliary equipment is a vital element in the design process and requires advanced modelling capabilities.
In comparison to commercial ship design, naval vessels are more complex. This is due to their smaller size, the requirement for high strength structures and the need for advanced operational capabilities. By using 3D modelling, Fincantieri was able to access the intricate level of detail required, reduce errors and avoid the design process becoming too labour intensive.
NAPA Solution
In 2003, NAPA Steel enabled Fincantieri Navy division to take the initial step to 3D structural design.
Over time, Fincantieri has revaluated and adapted its entire design process. By redesigning the whole process, Fincantieri achieved faster 3D modelling, automation of repeating tasks and the ability to customise the output from the software to correspond to the needs of the entire organisation. This means a core team of 2-3 engineers can feed the rest of the organisation with up-to-date information from the very beginning of the design process.
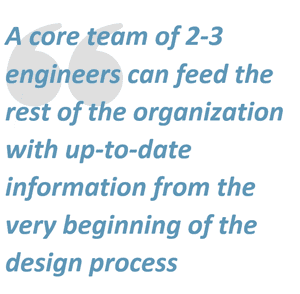
Accurate information exchange between different teams and design disciplines is crucial at Fincantieri, as throughout the design process there are many people in different teams involved in certain areas of the design. With this in mind, it is extremely important to communicate the latest stage of the design to the whole organisation to ensure every designer is working using the same revision, saving valuable time and money, reducing errors and streamlining the design process.
From the beginning, NAPA was able to tailor its offering for Fincantieri by conducting a thorough needs analysis. Likewise, NAPA was able to speed up the entire design process through the customization of the software. This helped for example to manage huge amounts of information and ensure that the output is in the format required by the user, i.e. Excel spreadsheet, multilayer graphic model and FE model. Fincantieri was also able to set up integration with Bentley Microstation, transferring the NAPA steel model, into the 3D and 2D Microstation model enabling the replication of all layers, line styles and colours. In addition, it was also able to reproduce the work-breakdown structure list in Fincantieri standard to be used as a reference for weight check and estimations.
Since then, NAPA and Fincantieri have collaborated closely. Fincantieri designers have been able to customise the software for their needs for over twenty years. The same macros and customisation are still in use today, helping the designers in their work and feeding the whole organisation with valuable information. Fincantieri has built up customisation to integrate NAPA Steel’s 3D model into Microstation to help the rest of the design engineers in their daily work. In the same way, up-to-date design information is automatically fed into Excel spreadsheets, 2D drawings and FE mesh, to support the rest of the organisation with vessel design. Fincantieri users have been the pioneers in cultivating NAPA functionality, with the actual Shell Landing tool in NAPA Designer, for example, developed in 2015 following the feedback from Fincantieri’s end-users of the software.
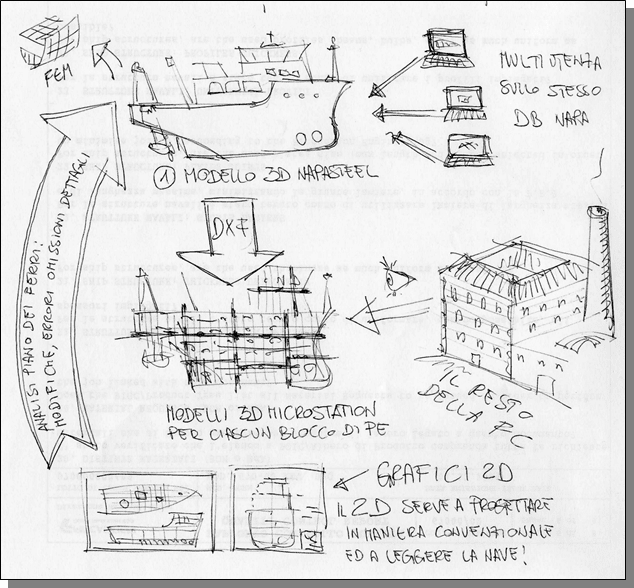
Today NAPA Steel plays a central key role in the contract and basic design phases at Fincantieri. Weight and material calculation is based on NAPA Steel as well as the space reservation of main components. The NAPA Steel 3D model acts as the central repository for design-related information, which is shared among all relevant shipyard stakeholders, as well as external stakeholders like the shipowner. The functional design in Microstation is based on a 3D model originating from NAPA Steel via the direct interface. The FE analysis is also based on mesh coming directly from NAPA.