April 28, 2020
Managing design complexity for Genting’s cruise ships with NAPA Steel
Background
MV Werften is a leading shipbuilding company that operates across three facilities in Germany on behalf of its parent company, Genting, and Genting’s three brands: Star Cruises, Dream Cruises, and Crystal Cruises.
Globally the cruise business has been experiencing strong growth. A substantial number of new cruise vessels have been built over the last 15 years, and the demand seems to remain strong.
However, there are only a limited number of facilities throughout the world that can meet the design requirements of discerning passengers and the complex naval architecture and safety challenges that passenger vessels inherently present.
By bringing its ship construction team in-house through MV Werften, Genting acquired the ability to build its own vessels as and when it needs them, and to incorporate the latest designs as they’re being built.
As a leader in ship construction and aware of the opportunities that demand growth presents, MV Werften is constantly looking to ensure that it is operating as efficiently and effectively as possible to deliver the ships that Star Cruises, Dream Cruises, and Crystal Cruises need.
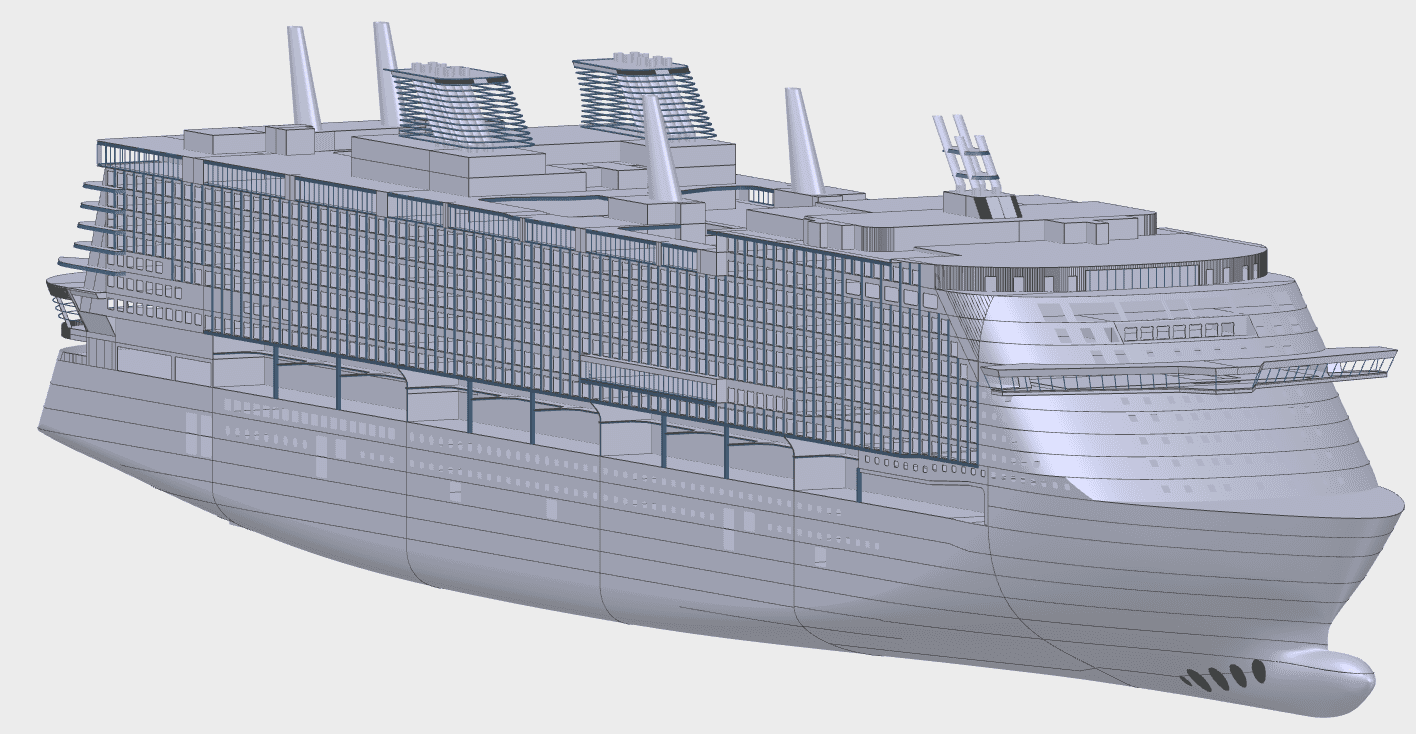
Approach
The design of cruise vessels, such as the 208,000gt “Global Class” cruise ship for Dream Cruises, is an enormously complex task. It requires many disparate disciplines, each with their own highly technical requirements to be developed in tandem, and then integrated into one common structure.
Moreover, innovative and novel designs are needed to meet the evolving demands of cruise customers and differentiate Star, Dream, and Crystal cruises within their respective niches. In recent years this has e.g. included almost an entire theme park onboard one vessel.
As designs have evolved, so has MV Werften. The company has begun to transition from the traditional design spiral to a more overlapping design process. However, this comes with its own implementation challenges. MV Werften has three locations for fabrication, around 500 engineers working at any one time, up to 600 design and construction partners, and each ship may have up to 20,000 documents associated with its construction. Furthermore, on average, for each ship may often have more than 250 changes to its original design during the build that will need to be realized.
In recent years, three major lessons were learned:
– Creating and using independent general arrangement plan (GAP), steel and strength models is not effective
– A strength calculation model cannot be used to communicate effectively with interior designers, the machinery and outfitting teams, and architects
– Structural design and strength calculations need to be sufficiently fast to allow for rapid evaluation of variants
Inspired by the conversations he’d had with NAPA staff and fellow naval architects and designers at NAPA’s User Meeting in 2017, Dr. Michael Zimmermann, Head of Calculation Services at MV Werften, first sketched out an idea to eliminate these roadblocks during his plane journey home from Helsinki.
After landing back in Germany, Dr. Zimmermann worked together in partnership with NAPA to develop a new approach for MV Werften to enable it to execute a more streamlined concept and basic design process in NAPA Steel.
Solution
Through the use of NAPA Steel, one central model is created which can be successfully used as the common basis for all major steel design and strength checks. Additionally, it can also be linked directly to the general arrangement plan and to a shipyard’s own product data model. This model can then also serve as the baseline for refined and accurately modeled investigations of each vessel’s interior, outfitting, and for its machinery.
With this approach, all major disciplines are tightly tied together and respective models for investigations are kept aligned by using the same model, without the risk of creating multiple competing versions. This leads to improved data integrity and data consistency but also to a reduced error rate in design.
The C# scripting in NAPA Designer is also heavily used at MV Werften to define and automate many tasks. By integrating it within NAPA Designer a higher design speed can be achieved, and reaction times when required design changes arise are significantly reduced.
Results
In the 55 years between 1940 and 1995, the record for the largest passenger ship changed hands twice. In the 24 years since 1995 that record has been broken 11 times. With additional size comes additional complexity, and it’s no different for the design process.
Dr. Michael Zimmermann, Head of Calculation Services at MV Werften, commented, “By working with NAPA, we have delivered improvements to our processes and measurable efficiency gains even as the intricacy and sophistication of the vessels we build has hugely increased.”
He continued, “NAPA Steel has been successfully introduced as a central tool for concept and basic design at MV Werften, and we have demonstrated that it is a more effective tool than the commercially available alternatives because models are aligned and consolidated, and more information can be delivered in a language everyone can understand.”
As a result of these changes there are less errors as quality and accuracy are built into processes, and there is a significant improvement in design speed and for implementing changes. Moreover, MV Werften anticipates huge additional potential to further improve speed and accuracy through automation in C# scripting.