September 6, 2021
Hyundai Heavy Industries and NAPA are innovating 3D structure design process together
Implementation of NAPA Steel streamlines the design process by providing a more agile and sophisticated platform for designers to collaborate on
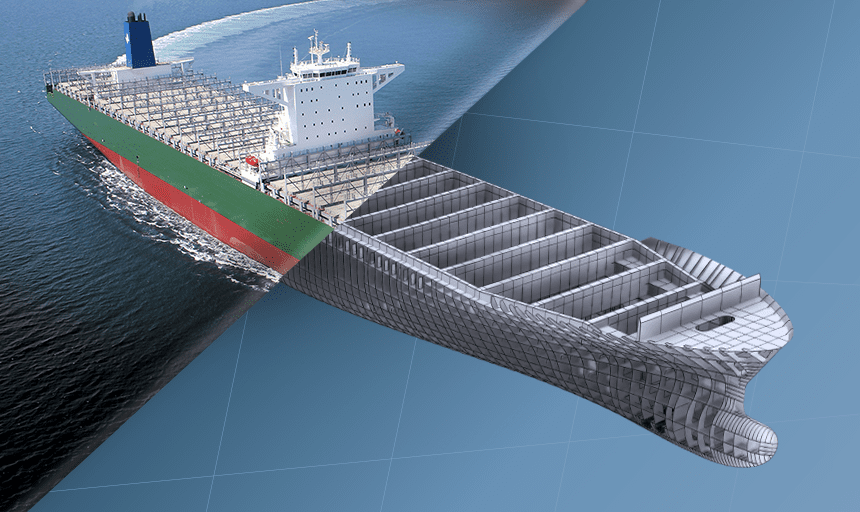
Background
In 2016, Hyundai Heavy Industries (HHI), the world’s largest shipyard, implemented NAPA Steel’s 3D model-based ship structural design tool across its Basic Hull Design Department. This marked a paradigm shift for HHI – it facilitated a move away from 2D drawing-based process. NAPA’s interactive 3D structural modeling interface allowed users to create a single flexible model for a whole vessel. HHI used these models throughout the basic hull structure design process, including class society rule checks, creating plan approval drawings, Finite Element model generation, weight calculation, and many other tasks.
By linking structural design databases and drawings to the NAPA 3D model, design quality was improved, and the probability of human error was reduced, as common information was shared and the update process became simpler.
Challenge
Before this shift, HHI’s design process was based on the traditional 2D approach. In this approach, 2D drawings played a central role in sharing information between different stakeholders, with 2D drawings acting as an intermediary for manual information exchange between sections for rule checks and FE models.
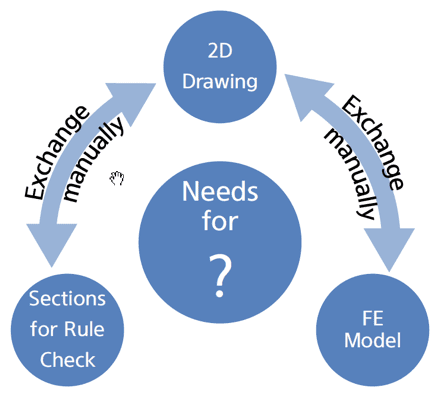
Although this process was familiar and had a long track record, in 2016, HHI found itself in a situation whereby it, like many other yards around the world, had to create completely new ship designs and renew its processes to comply with changing regulations and ship owner’s evolving requests. The more sophisticated design software was therefore required.
NAPA solution
After a long process of evaluation, NAPA Steel delivered significant advantages, namely:
One Integrated Database
- Includes all information about weight, painting area, welding length, etc.
- The same information is available to all users
- Easy to extract FE model and rule interface
- Easy to create the plan approval drawings
Flexible Model
- Easy modification of design parameters, hull form, frame spacing, and primary members
- A quick review of design alternatives for optimum hull structure design
Information Sharing
- Allows other departments to reference 3D data (Detailed Design, Outfitting Arrangements)
- Offers an intuitive 3D view to understanding complicated structures
Fit for the design process
- Flexible design tools make it possible to create the 3D model already in the pre-contract phase
- Weight estimation and other benefits are available then already in ship contract negotiations
Results
Since this was implemented in 2016, both NAPA and HHI have constantly been iterating and improving the design process and collaborating to find the most effective ways to use NAPA. The results are notable:
HHI has saved valuable design manhours from FEM, Drawings, and Rule Software Interface in new building projects
Specifically, models for DNV’s Prescriptive Rule Check, Geometry, Plate and Stiffener, etc., had all previously needed to be modeled manually before switching to NAPA. With NAPA Steel, sections for rule scantlings can be created automatically from NAPA Steel model with minimal touch-up.
Likewise, it was difficult for designers to estimate weight variations according to design changes in the 2D drawing-based process. This is now easier with NAPA Steel.
The quality of work has also increased, with inconsistencies between drawings resolved faster and more accurately. NAPA Steel has also helped convey accurate design information to the next design stage (Detail Structure Design) and made it easier to reflect improvement and feedback from the detail design.
Overall, this now means that HHI is much closer to making 3D model-based approval a reality. This method of approval is recognized by shipyards, classification societies, and software suppliers as an essential evolution in ship design. In a recent paper co-authored by NAPA for ICCAS, we found that there are specific issues that stem from the division of design work between different stages of 3D modeling, 2D drawing, rule calculation, and direct strength calculation. Designers needed to carry modifications across all stages each time they occurred. Likewise, structural designers needed to use different software at each stage. This not only increased their workload but even required multiple people to split up the tasks by using different software applications. Discrepancies occurred between the 3D CAD model and the models used for rule checks. Significantly, it meant that structural designers didn’t have an overview of the whole process, making it hard to optimize the overall design.
Conclusion
Ultimately, this division between 3D design and 2D rule checks restricts the design possibilities for ship designers. It introduces unnecessary friction to the design process and encourages siloed work, with separate teams working on different models with different software applications. Ships are three-dimensional objects, and we need to be able to design and assess them accordingly – and the shift to 3D model-based approval makes this far easier.
There is still a long way to go to fully integrate the 3D model into HHI’s design process, and further efficiencies to be realized. One of the challenges HHI sees in the current 3D design process is that 2D drawings are still used by other stakeholders like Class Societies and Ship Owners. Drawings are still the basis for the design approval from the shipowners and classifications, and they will exist within the 3D design process for a while. In addition to easy drawing generation from 3D, HHI and NAPA cooperate with Classifications first to establish the fully 3D Model-Based Approval process.
HHI is committed to accelerating the paradigm shift of the 3D design process. The route ahead is clear; adopting a 3D model-based structural design is already saving significant time, reducing errors, and setting HHI on a course for a far more streamlined and robust design process.
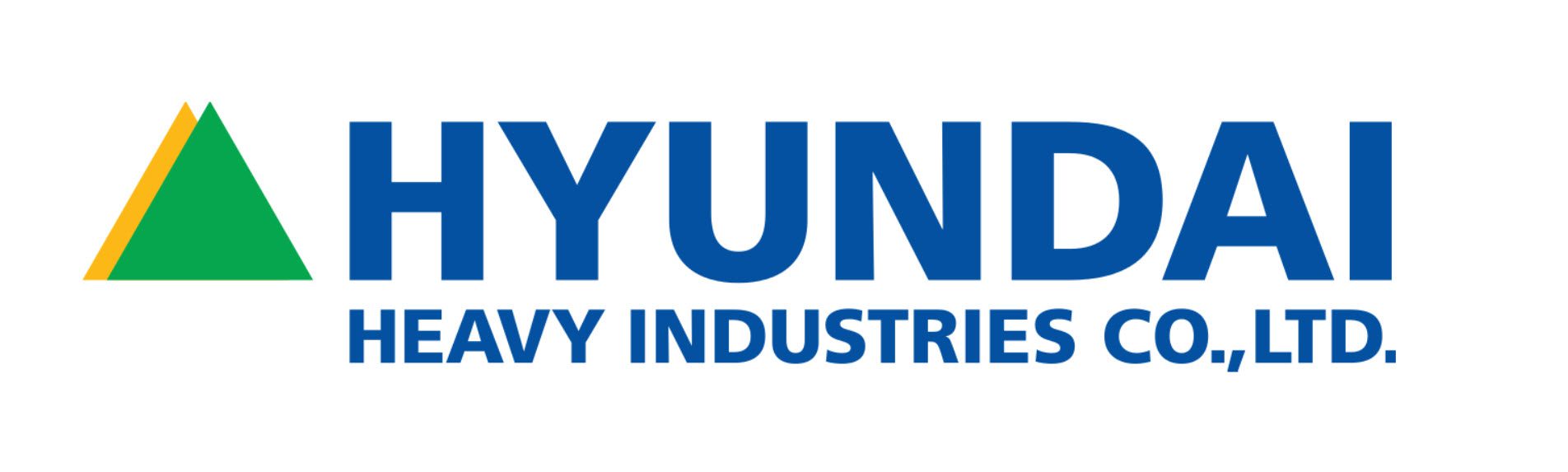
Case HHI in a nutshell
Background
HHI required a more dynamic and agile 3D modeling tool to support increasingly complex vessel design. Implementation of NAPA Steel’s 3D model-based ship structural design tool revolutionized HHI’s ship design process by upgrading from 2D to 3D modeling.
Challenge
HHI’s design process was originally based on the traditional 2D approach. While effective, it no longer fulfilled new market demands for increasingly complex vessel design. The more sophisticated 3D design software was therefore required.
Solution
NAPA Steel delivered significant advantages. The main advantages being one integrated database, flexible model, and information sharing. NAPA and HHI continue to collaboratively iterate and improve the design process to find the most effective ways to use NAPA.
Conclusion
With NAPA Steel, HHI has streamlined its design processes – saving valuable design manhours and reducing errors from FEM, Shell Expansion Drawing, and Rule Software Interface processes in new building projects.